Is Spot Welding Stronger Than MIG Welding
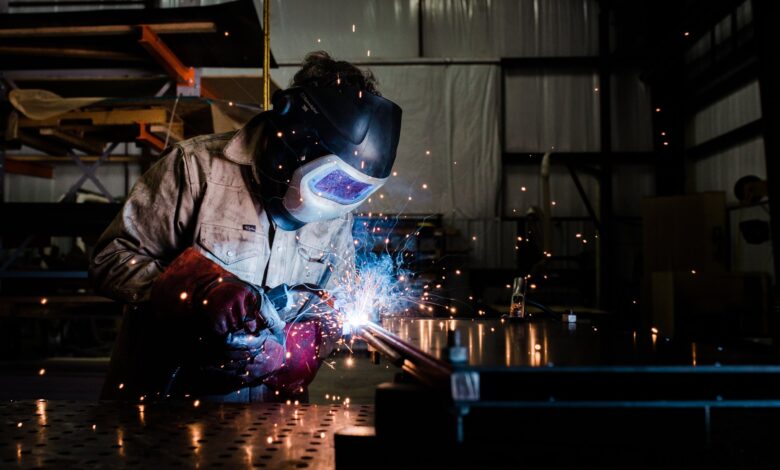
Welding is an important joining process in metal fabrication. It is a permanent method that ensures strength and integrity for the final part. Of the welding techniques available, spot and MIG welding are the most common. They are effective methods and you can use them across various manufacturing industries.
As a beginner or seasoned welder, it is common to wonder if spot welding is stronger than MIG welding. The answer to this question lies in understanding how both processes work, their strengths, and limitations. This article will explain what spot welding vs MIG welding, the factors affecting their weld strength, and help you determine which welding method is stronger.
What is Spot Welding
Spot welding is a type of resistance welding. It forms a bond between two metal sheets without the need for filler materials. The process of spot welding is straightforward even for novices. The first step involves placing the workpiece between two copper electrodes. You then apply pressure and allow electric current to flow through the metal sheets.
The resistance to the flow of current generates heat and causes the metal to melt. As they cool and solidify, a weld nugget or button is formed that fuses the parts firmly. Spot welding is fast and you can use it to join dissimilar materials. However, this welding process is best suited for metals with high electrical resistivity and low thermal conductivity.
Factors Affecting Spot Welding Strength
Several factors affect the strength of spot welding. Some of these factors include
Material Thickness
The thickness of the metal you are working with will affect the strength of the weld nugget. Go for metal sheets with thicknesses ranging from 0.2 to 1 inch. Thin metals are susceptible to overheating and burn through. For metal sheets thicker than 1 inch, you may experience uneven heat distribution and insufficient heat penetration.
Electrode Condition
The electrode pair you are using plays an important role in spot welding. The electrodes must be clean and free of debris to ensure sufficient transfer of heat. Furthermore, the tip of the electrode should be clean, flat, and properly maintained to avoid weakened joints.
Surface Preparation
The level of surface preparation is also important. You must clean the metal sheets before carrying out the spot welding operation. Dirt, dust, and other contaminants can interfere with the flow of current and result in poor fusion. Additionally, these contaminants can undergo unwanted reactions that can affect the weld integrity.
Welding Parameters
The welding parameters you use will determine the strength of spot welding. For different metal types and thickness levels, you ought to optimize parameters such as pressure, current, and time to avoid mistakes. Too low than the required current and pressure can lead to incomplete fusion. Furthermore, using insufficient welding time will not allow the joint to melt completely.
Cooling Rate
The rate of cooling has a significant effect on the strength and quality of the final weld. Cooling the joint too fast increases the strength and hardness. However, the weld may become brittle over time. On the other hand, too slow a cooling rate will affect ductility and reduce the hardness level. There should be a balance for the best results.
Alignment and Fit-up
The way you align the workpieces and the electrodes makes a lot of difference. Proper alignment and correct fit-up ensure that the current and pressure penetrate deeply and evenly in the right spot. Where there is misalignment or unwanted gap, the joint may be weak and prone to many welding defects.
What is MIG Welding
MIG (Metal Inert Gas) welding is a popular process that uses a consumable wire electrode to join metal parts. This technique is compatible with many materials including copper, aluminum, steel, and nickel alloys. You carry out MIG welding by continuously feeding in an electrode through a gun.
When current is supplied, an electric arc is formed between the electrode and the workpiece. The arc generates the heat needed for the welding operation. The electrode and the base metals then melt and solidify on cooling. In the MIG welding process, it is important to use an inert gas to shield and protect the joint from contamination.
Factors Affecting MIG Welding Strength
The following factors affect the strength of a final MIG weld
Gun Distance and Position
The position and distance of the welding gun from the workpiece affect the strength and quality of the final weld. The gun distance should be between ¼ to ¾ inch for proper heat distribution and arc stability. Furthermore, place the gun at around 5 to 15 degrees in the direction of motion for optimal heat input.
Electrode Type and Diameter
The size and type of electrode you are using are also important. MIG welding wire can either be the flux-cored or solid type. You should consider the workpiece material and intended application before using any. Furthermore, choose the diameter of the electrode based on the thickness of the workpiece. Using a smaller or larger than required electrode will affect MIG welding strength.
Shielding Gas
The type of shielding gas and the total gas coverage are essential factors. You can use pure argon or argon-CO2 mixture during a MIG welding operation. Go for pure argon when working with aluminum and other nonferrous metals. However, an argon-CO2 mixture is ideal for welding steel. Furthermore, ensure that there is adequate gas coverage to avoid pores in the final weld.
Material Type and Thickness
MIG welding is compatible with many engineering materials. However, you should not use it for heat-sensitive ones like high alloy steels. For this metal, you may experience burn-through during the welding process. The thickness level of the metal is also important. MIG welding works best with thickness ranging from ¼ to 2 inches based on the metal in question.
Voltage and Amperage
The voltage and amperage you use during MIG welding will affect the weld strength. You should optimize the voltage based on the workpiece material. Too high voltage will lead to spatter while too little will cause poor penetration. Furthermore, use the right amperage to avoid warping and weak welds.
Wire Feed Speed
Do a proper calculation of the wire feed speed before starting an operation. A higher-than-required speed will increase heat input and the size of the weld pool. The result is a thick but compromised joint. However, reducing the deposition rate of the filler material will lead to inadequate fills and weak welds.
Comparing the Strength of Spot and MIG Welding
When comparing the strength of spot and MIG welding, many factors come into play. MIG welding is stronger than spot welding in many instances. Let’s analyze spot and MIG welding strength in terms of the following
Tensile Strength
The tensile strength of MIG welding is considerably higher than that of spot welding, especially for thick materials. This is because MIG welding provides a continuous welding action with full penetration. For spot welding, the tensile strength of the weld is lower than that of the base metal.
Impact Resistance
The impact resistance of spot and MIG welding is also different. MIG welds have a higher impact resistance and do not break down when you use them in demanding applications. This is because MIG welds cover a larger area which can absorb and distribute impact force efficiently.
Shear Strength
When it comes to the amount of shear strength the weld can withstand, spot welding stands out. Spot welds have a higher shear strength because the heat is concentrated in a small area. This creates a strong and dense weld nugget making it suitable for high load applications.
Fatigue Resistance
The fatigue resistance of spot and MIG welding differs. MIG welds have a higher fatigue resistance. This implies that they can survive in places where repeated loading and unloading is needed. The high fatigue resistance of MIG welding is because of the favorable grain structure and lower residual stresses it produces.
Conclusion
Spot and MIG welding are two important techniques for joining two or more metal parts. They have unique advantages, disadvantages, and applications. When doing a spot weld vs MIG weld comparison, MIG welds stand out. MIG welding offers higher tensile strength, impact resistance, and fatigue resistance making it suitable for many applications. In addition to strength, you should also consider the heat-affected zone, material compatibility, and weld quality when choosing a welding technique.